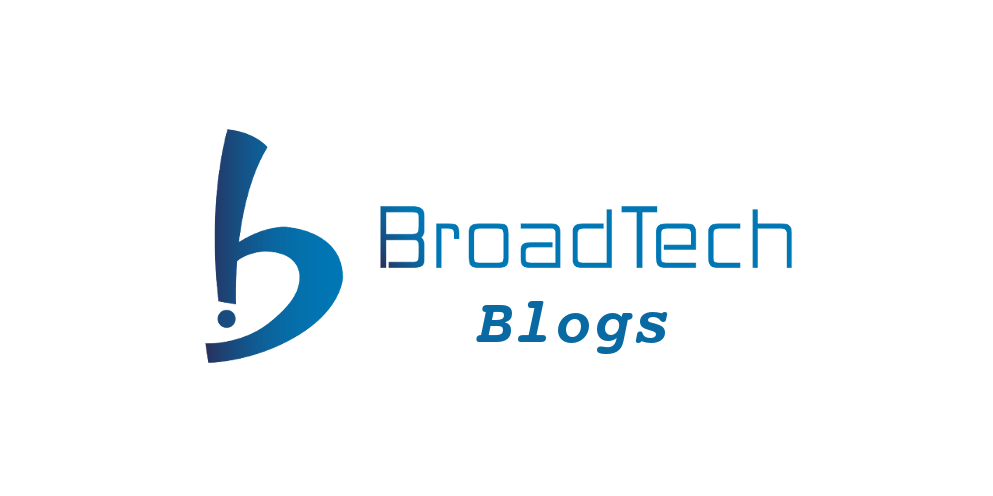
Weekly Purchase Orders in Odoo
Scenario : When the company receives sales orders from customers to deliver products, it issues purchase orders to vendors. Company receives products from vendors(suppliers) against the Purchase Orders and then delivers the products to the customers based on sales orders. In our scenario almost all the sales orders of the company are created in the initial months of the year even though delivery dates of the orders ranges from the first month of the year to the last month of the year.
The article describes how purchase can be managed using standard Odoo process flows, what are the drawbacks of the standard process and how the drawbacks can be overcome using customized Odoo process flow.
Standard Process – Sale Order to Purchase Order : flow 1
1 ) Products are configured with Routes and Suppliers. The routes “Make to Order” and “Buy” means the product would be purchased if demand for the product appear in the form of sales orders or manufacturing orders. The purchase orders for this product would be created automatically based on the supplier configured in the product.
2 ) Sale Order SO017 is created. The date of the sale order is June 3, 2019. Sale Order line is for 1 unit of Product A
3 ) Delivery Order is created automatically . The scheduled date of the delivery order can be seen as June 3, 2019
4 ) Procurement Order also would be created automatically based on route configuration of the product
5 ) Procurement Order would run either automatically based on the scheduler or it can be run manually
6 ) “Running” the procurement order would create PO, MO or stock moves based on route configuration of the products. In our example, it would create or update a PO, by identifying the supplier.
- If there is already a draft PO for the supplier of the product ( Product A and ASUSTeK) , the procurement order adds the product into the draft PO.
- If there is no draft PO for the supplier, the procurement order creates a new PO
7 ) Here, it creates a new draft purchase order . The scheduled date of the procurement order can be seen as June 3, 2019.
8 ) New draft PO got created since there were no draft POs against the supplier “ASUSTeK” who is the only supplier of “Product A”
Standard Process – SO to PO : flow 2 – Different Delivery Dates
Here we are repeating the entire process with another product and another scheduled date
1 ) A new product, Product B, with the same route and supplier configuration is considered here.
2 ) Sales order SO018 is created with 1 unit of Product B on a different order date – June 10, 2019
3 ) Delivery Order is created automatically. The scheduled date of the delivery order can be seen as June 17, 2019 (Order Date + Customer Lead Time of the product)
4 ) Procurement order is created
5 ) Created procurement order is run after execution of mrp scheduler.
6 ) “Running” the procurement order would create PO, MO or stock moves based on route configuration of the products. In our example, again, it would create or update a PO, by identifying the supplier.
- If there is already a draft PO for the supplier of the product ( Product B and ASUSTeK) , the procurement order adds the product into the draft PO.
- If there is no draft PO for the supplier, the procurement order creates a new PO
7 ) This time, it didn’t create a new draft purchase order, but updated the existing PO with the new product ( Product B, 1 Unit ) . The scheduled date of the procurement order can be seen as June 17, 2019.
8 ) The existing purchase order, PO00015, into which Product B was added, shows the sources of the order as SO017 and SO018
Standard Process – SO to PO : Drawback
The standard Odoo process has a drawback in the scenario we are discussing. Since sale orders for the entire year are created within a few days during the starting of the year, the Purchase order creation would happen as mentioned in section 6.a of flow 1. Which means, there could be only one PO for one supplier, containing all the products required to be delivered during the year. This is inconvenient. In broader sense the company has to issue a big Purchase order against all the sales orders. Same PO for the Sales orders to be delivered in the first month and last month of the year.
Custom Process – Weekly PO
The custom solution in Odoo would create separate draft purchase orders for one supplier if the delivery dates of the products varies. All the products to be delivered on a particular week will be part of one Purchase Order. New POs would be created on a weekly basis. One Purchase Order for one supplier in one week.
1 ) First Sale order SO020 with Order Date June 17, 2019 and Product A in order line. Supplier of Product A is ASUSTeK
2 ) Second Sale order SO021 with Order date June 24, 2019 and Product B in order line. Supplier of Product B is also ASUSTeK
3 ) Running the Procurement order corresponding to SO020 (first SO) creates a new Purchase Order, even though there was already a draft PO for the supplier ASUSTeK
4 ) Running the Procurement order corresponding to SO021 (second SO) creates a new Purchase Order, even though there was already two draft POs for the supplier ASUSTeK
5 ) Two consecutive procurement created two different draft purchase orders for the same supplier, just because the expected delivery dates of the products in sale orders belonged to two different weeks.
6 ) The list shows 3 draft purchase orders for the supplier Austek. In standard case, Odoo would have created only one draft PO. The difference is a result of the customization to generate weekly Purchase Orders for each supplier based on delivery dates of the product as per the sales orders.
Following YouTube video explains the process in detail.